biline's blog
History behind the biline.ca website
Have a laugh read the Humour Pages
Read or sign my Guestbook
Read about the IBM 4100 Web-printer
Customer Service where has it gone?
Why should we trust your reviews?
Renovation Tips and advice for your health and wallet!

|
|
Let's move on to the actual renovations
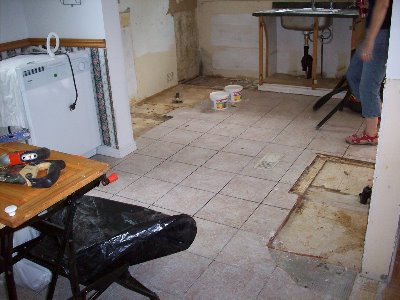 |
Here is the kitchen area after most of the cupboards were removed, we decided to ditch the tiles as we planned on moving the vent from the middle of the floor and a few tiles were cracked. I was very lucky to have my fathers help in this endeavor as we needed to remove the tiles and the layer of plywood that the tile had been affixed. I purchased a couple of long wrecking bars for the purpose and with the two of us prying constantly we slowly managed to remove all the floor, it took us most of the day. I think more time was spent removing nails that we missed while pulling sections of the floor off. |
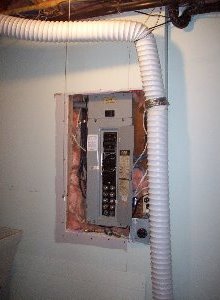 |
You can see the original electrical box in this photo was using fuses now I don't think they are unsafe but I wanted an electrical panel with breakers. I hired a local electrical contractor to perform the work as I was not about to try and tackle this job. The house was built over thirty years ago so finding fuses was not a complete surprise and at least the wiring was all copper. Thankfully I did not have to deal with the problems of having aluminum wiring. For the price of $1,388.15 they replaced the electrical panel and moved the dryer plug and relocated the stove plug. The extra cost for wire and new outlets was mine. I purchased the items needed in advance from the local Home Depot for $54.06
You can't see the dryer in this picture but the original layout had the washer next to the sink and the dryer in front of the sink which was attached to the very unsafe length of plastic dryer hose vent. |
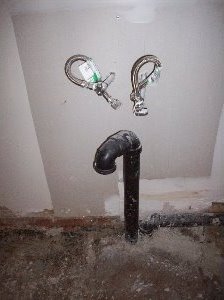 |
The basement bathroom floor was very unlevel so we filled all the lower sections and tried our best to level the area with repeated applications of cement. After the fourth time it was pretty good and we filled in that gaping hole around the shower stall pipe in the floor. You may have noticed it but if not you can have a look Here, the toilet has this weird enclosure behind it to accommodate the pipe that leads to the vent stack (photo on the left). We decided to run the pipe through the existing wall, we removed the last 8" of drywall then cut through the 2x4's (not holding anything except drywall) we cut a gap large enough for the ABS pipe and cut and reran the vent pipe inside this gap. Once done I used some metal braces on each side of the 2x4's to ensure nothing would move and we used a product called "Easyboard" instead of drywall to patch the wall. This product cuts cleanly with a knife and feels like foam core board but unlike drywall produces liitle dust. |
That Covers the Lower level of the House so lets head up to the Kitchen Next Page >
<< Back | Next >>
|